Does Removing Oxygen from Coolant Prevent Chiller Corrosion? The Science & Solutions
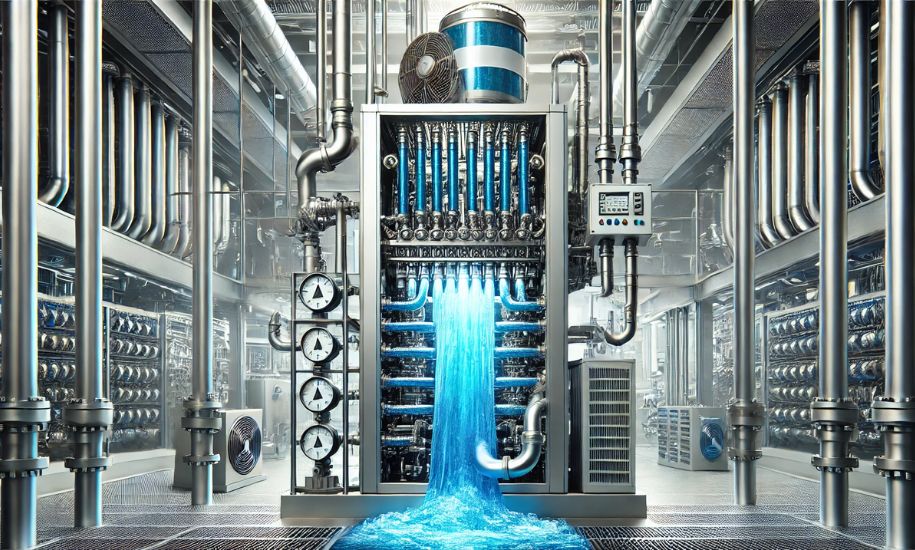
Chillers are critical components in industrial and commercial HVAC systems, helping maintain temperature control in large-scale operations. However, one of the biggest challenges in chiller maintenance is corrosion, which can significantly reduce the system’s efficiency and lifespan. One commonly proposed solution to this issue is the removal of oxygen from the coolant. But Does Removing Oxygen from Coolant Prevent Chiller Corrosion? In this article, we will explore how oxygen affects chiller systems, the benefits of oxygen removal, and the best methods to achieve a corrosion-free cooling system.
Understanding Chiller Corrosion
Corrosion in chillers is primarily caused by the interaction of metal surfaces with water, air, and other contaminants. The presence of oxygen in coolant accelerates oxidation, leading to rust formation, pitting, and structural degradation. Common materials used in chillers, such as copper, steel, and aluminum, are all susceptible to different types of corrosion, including:
- General corrosion – A uniform deterioration of metal due to oxidation.
- Pitting corrosion – Localized damage that leads to deep holes and leaks.
- Galvanic corrosion – Occurs when two dissimilar metals are in contact with an electrolyte.
- Microbiologically influenced corrosion (MIC) – Bacterial activity that exacerbates metal degradation.
Given these risks, minimizing oxygen exposure is crucial in maintaining chiller efficiency and preventing costly repairs.
How Does Oxygen Contribute to Corrosion in Chillers?
Oxygen plays a significant role in accelerating the corrosion process in chiller systems. When dissolved oxygen is present in the coolant, it reacts with metal surfaces, forming iron oxide (rust) and other corrosion by-products. This reaction weakens metal structures and can cause leaks or complete system failures. Here’s how oxygen contributes to chiller corrosion:
- Oxidation Reactions – Oxygen molecules react with metal surfaces, leading to rust and material degradation.
- Formation of Acidic Compounds – Oxygen can contribute to the formation of acidic compounds in the coolant, increasing its corrosive potential.
- Localized Pitting – In oxygen-rich environments, localized pitting can occur, forming deep holes that compromise the chiller’s integrity.
- Microbial Growth – Oxygen supports the growth of bacteria, fungi, and algae that can further deteriorate metal surfaces.
Does Removing Oxygen from Coolant Prevent Chiller Corrosion?
The answer is a resounding yes. Does Removing Oxygen from Coolant Prevent Chiller Corrosion? Removing oxygen from coolant significantly reduces the risk of corrosion by eliminating one of its primary catalysts. By deoxygenating the coolant, metal components remain in a more stable environment, thereby increasing the chiller’s lifespan and improving overall performance.
Benefits of Oxygen Removal in Chiller Coolant
- Extended Equipment Lifespan – Reduced oxidation means metal parts last longer, decreasing the need for frequent replacements.
- Lower Maintenance Costs – Preventing corrosion helps avoid costly repairs and system downtime.
- Improved Thermal Efficiency – Corrosion buildup can reduce heat transfer efficiency. By eliminating oxygen, the system maintains optimal performance.
- Minimized Risk of Leaks – Corrosion-induced leaks are a common problem in chillers. Oxygen removal helps keep the system sealed and intact.
- Enhanced Effectiveness of Corrosion Inhibitors – Many corrosion inhibitors work best in low-oxygen environments, making them more effective when oxygen is removed.
Methods for Removing Oxygen from Coolant
Several techniques can be used to eliminate oxygen from coolant in chiller systems:
1. Chemical Oxygen Scavengers
Chemical treatments are one of the most common ways to remove dissolved oxygen from coolant. These chemicals react with oxygen, neutralizing its corrosive effects. Common oxygen scavengers include:
- Sodium sulfite – Commonly used in industrial systems to remove oxygen.
- Hydrazine – An effective but highly toxic chemical used in high-pressure applications.
- Ascorbic acid – A safer alternative that binds with oxygen to prevent oxidation.
2. Deaeration Techniques
Mechanical deaeration physically removes dissolved gases, including oxygen, from the coolant. Two main types of deaeration systems are:
- Vacuum deaeration – Uses a vacuum pump to remove gases from the coolant.
- Spray-type deaerators – Utilize a spray system to release dissolved gases into the atmosphere.
3. Nitrogen Blanketing
Nitrogen blanketing involves introducing nitrogen gas into the chiller system to replace oxygen. This technique is highly effective because nitrogen is non-reactive and prevents oxygen from dissolving back into the coolant.
4. Boiling and Degassing
Heating the coolant to remove dissolved gases is another effective method. Boiling forces oxygen out of the liquid, which is then removed through degassing equipment.
Best Practices for Preventing Chiller Corrosion
Apart from removing oxygen, additional best practices should be followed to minimize corrosion in chiller systems:
- Use Corrosion Inhibitors – Add inhibitors designed to protect specific metals used in your chiller system.
- Monitor Coolant Chemistry – Regularly test the coolant for pH balance, oxygen levels, and contaminants.
- Maintain Proper Water Treatment – If water is used as a coolant, it should be properly treated to remove impurities.
- Ensure Proper System Sealing – Prevent oxygen from entering the system by ensuring all pipes, tanks, and connections are airtight.
- Schedule Regular Maintenance – Routine inspections help identify early signs of corrosion and prevent major failures.
Conclusion
So, Does Removing Oxygen from Coolant Prevent Chiller Corrosion? Absolutely. Oxygen plays a major role in the deterioration of metal components within chillers, leading to reduced efficiency, increased maintenance costs, and potential system failures. By implementing oxygen removal techniques such as chemical scavengers, deaeration, nitrogen blanketing, and proper system sealing, businesses can significantly extend the life of their chillers and improve overall operational efficiency.
For more insights on industrial maintenance and technology, check out Mating Press, where we cover essential topics related to equipment performance and system longevity.